
Tips for how to select the right one for your application
Worm Gear Screws Jacks can provide long duty life, high load capacity and flexible design. They come in two major categories, Ball Screw and Machine Screw. In this post, we hope to help you identify the best type for your application.
Ball Screw Jacks use a ball screw and nut made from hardened alloy steel with bearing balls carrying the load between nut & screw. This rolling action reduces the friction between nut and screw, permitting smooth and efficient load movement that requires approximately 1/3 less torque than a machine screw jack with the same load.
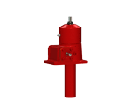
Machine Screw Jacks incorporate an alloy or sometimes stainless steel worm which drives a high strength bronze worm gear, or drive sleeve. The worm shaft is supported on anti-friction tapered roller bearings with external seals that prevent lubrication loss. The drive sleeve can also be supported on tapered roller bearings, or ball thrust bearings. Rotation of the drive sleeve causes the acme thread lifting screw to translate or rotate, depending on the jack configuration.
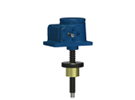
Because of their efficiency and lower power requirements, Ball Screw Jacks are often preferred. However, several factors can make Machine Screw Jacks preferable. For quick reference …
Machine Screw Jacks are best used for:
• Resistance to backdriving
• Environments with vibration
• Manual operation
• High static loads
• Corrosion resistance (with stainless steel versions)
Ball Screw Jacks are preferred for:
• Long travel lengths
• Long, predictable life
• High duty cycles
• Oscillating motion
Both types can be metric or inch, come in several types (Upright, Inverted, Upright Rotating and Inverted Rotating) and multiple jacks can be laid out in H, U, T and In-Line arrangement.
You can also employ multiple jacks in tandem, depending on the physical design and size of the equipment, its stiffness and the guide system. This will, however, introduce challenges with drive, alignment and synchronization.
Any jack system is limited by multiple constraints: load capacity, duty cycle, horsepower, column strength, critical speed, type of guidance, brake motor size and ball screw life. To properly size your jack for these constraints, application information must be collected.