All posts by admin
Flex Coupling 101
Jacks used alone or in multiple arrangements require couplings to transmit power to the input shaft. Traditionally, there are 3 types of couplings; Jaw Type, Alloy Sleeve and Carbon Fiber Sleeve .
Jaw Type
Jaw Type couplings are made of two steel hubs and a flexible polymer insert.
This type is a common coupling option for close mounted arrangements, or in arrangements where the radial loads are being supported with the proper placement of a pillow block support bearing. An example would be a direct coupling of a motor or gearbox to an adapter flange mounted on the jack, or when a mounting line shaft is supported with radial pillow block bearings mounted close to the coupling. It is, however, possible to use jaw couplings without a pillow block support, but only if the input is hand driven. In that case, deflection of the link shaft still needs to be considered with respect to the ratio of diameter to length.
Alloy Sleeve
Alloy Sleeve couplings are an industry standard for many jack arrangement applications. They provide a rigid mount that can eliminate the need for pillow block support bearings, while at the same time allowing for significant torque transmission through the system. The best styles will have both hub gears and outer sleeves made from alloy steel to provide a high degree of support and torsional strength.
They are available in both Full Flex & Flex Rigid styles,with Flex Rigid having a longer engagement with the outer sleeve than the Full Flex. This allows for the Full Flex to have greater misalignment, however the Flex Rigid can provide greater radial support and can be considered as a radial support. Because of this Full Flex couplings should be used for close coupled arrangements, and in the case of a floating shaft application, two Flex Rigid couplings can be employed, with the rigid half mounted on the floating shaft.
Carbon Fiber Sleeve
Carbon Fiber couplings are similar to the Alloy Sleeve in construction, but only in Full Flex styles and with reduced maximum torque, these couplings can be a cost-effective solution in the right setting, specifically ones where torque requirements are not significant and where considerations have been made with reference to radial supports.
Primary materials are alloy steel for hub gears and, as you might guess, an outer sleeve of carbon fiber. It is recommended that these couplings always use a supporting pillow block bearing. Occasionally, radial supports may not be needed based on operating requirements and in close mount arrangements.
With all styles, it is important to account for maximum angular and radial displacement. Below are the displacements by type;
Jaw Type – Angular 0.9°/Radial +/- 0.09mm (0.004″)
Alloy Sleeve – Angular 0.5°/Radial +/-0.13mm (0.005″)
Carbon Fiber Sleeve – Angular 1°/Radial =/-.3mm (0.012″)
Brush Up On the Basics
It never hurts to remember the basics, or have one easy place to find them when training others. Here’s an article from Design World that lays out some common terms.
Happy Thanksgiving!
This blog post from Tradesmen Insights sums it up nicely.
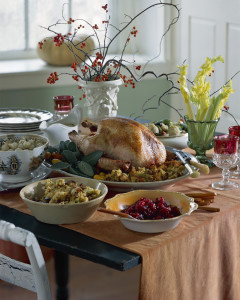
From everyone at Making Motion Work; have a great Thanksgiving!
Automation Fair 2015
Rockwell’s Automation Fair 2015 kicked off today in Chicago, and as usual, it sets the standard for the industry.
Unique in it’s position for facilitating complete solutions, Rockwell uses the Fair to show what’s new and next, while also setting the topics of conversation for the coming year. Seminars and meetings cover topics such as;
- Converging Operations with IT as more and more production becomes computer controlled
- The “Internet of Things” and how to use it to your advantage
- A kick-off diner last night that had over 300 attendees and was focused on Latin America
The Journal has excellent, real-time coverage on it’s Facebook page, and you can follow Nook’s coverage as well by clicking here.
If you’re in Chicago, enjoy the show. If not; make plans to attend next year in Atlanta.